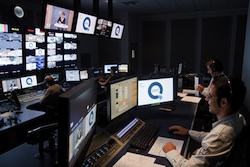
The corporate mantra of ‘Quality, Value, Convenience’ seems to apply as much to broadcasting facilities as the home shopping channel itself at QVC Italy, writes Richard Dean. This is the latest addition to the expanding QVC empire, which following its launch by Joseph Segel in his native US back in 1986 is now one of the largest multimedia retailers in the world, broadcasting to 160m consumers worldwide.
“We took over an old industrial building in Milan that was being dry-hired for TV commercials, large TV productions and still life photography,” says Mattias Bråhammar, vice president of TV Operations at QVC Italy. “There was no technology of any sort, as everything had to be brought in and rigged for each job, so we had to start from scratch.”
By the time the channel went to air on 30 September last, the space had been transformed into a state of the art HD production and broadcasting facility. But right from the start of project planning during the summer of 2009, it was clear that this was to be no ordinary installation.
“QVC has very specific needs, due to our particular way of using the studios,” says Bråhammar. “The biggest challenge distinguishing our operation from ‘normal’ TV production is that we change sets and product every hour, so there is a constant product flow to and from the studios, plus the guests and product specialists connected to each show. This requires the flexibility to accommodate not only planned show changes but also any equipment failures on a service broadcasting 24/7.”
After choosing TSL as the systems integrator in the early autumn, the decision was taken to build two identical control rooms for redundancy purposes, alongside four live studio floors totalling more than 950 sq m.
“We switch each day so that both galleries are used equally, and obviously use them for training and some off-line shooting from time to time, but this is a bonus – the main purpose is to ensure continuity. Solutions such as the TSL Tallyman is another example of this, as well as the actual studio layout with the ancillary areas around them, all designed to maintain and optimise the flow.”
Italy is the first QVC to use a rapid switching feature on the TSL Tallyman, which allows control to be switched between the different live facilities with a single touch screen command.
The project was divided into nine areas, three of which were due for handover last July with the other six due for September. In the event, TSL released seven areas in July, with the remaining two also delivered ahead of schedule. Development of the full specification and RFP process was an interaction between the different QVC international sites, led by John O’Neill of the QVC Japan Engineering team.
“Extensive help was also obtained from the QVC UK office, not least in the start-up training where different department specialists worked closely with the new QVC Italy team, as well as with the TSL team and their subcontractors,” says Bråhammar.
Interestingly, QVC Italy has one of the largest studio-based moving track lighting grid systems installed anywhere in the world. “In each of our live studios we have multiple sets for different product categories,” he explains, “which all need their own dedicated lighting, rigged and ready at all times. We also try to squeeze out several different configurations within each set, and all of these are kept ready for use at the touch of a button on the lighting desks.
“Our daily schedule not only calls for set changes each hour, but also during some programmes such as multi-category shows for example, so the amount of physical moving needs to be kept within practical limits. We actually worked hard to keep the number of lights down as much as possible to reduce power consumption. This is also why we went for mainly florescent lighting, using tungsten only for key lights and back lights, not only to reduce consumption but also the heat from HVAC systems.”
Graphics and MAM
Although broadcasts on terrestrial (LCN 26, 45), cable (streaming), Hotbird, Sky Italia (channel 475) and TiVu Sat (channel 34) currently go out only in SD, the whole facility operates in 1080/50i format with signals down-converted to MPEG2@3 Mbps CBR (Constant Bit Rate) format just before leaving the building. All interchange within the facility is file-based, as the facility is tapeless throughout.
For editing and finishing the company uses Quantel eQs with effects and Q Color options, as well as Final Cut Pro suites plus a dedicated Pro Tools audio suite, while a mix of Adobe suite workstations and 3D Studio Max for 3D handles the graphics.
The on-air graphics are played out by VizRT, but using bespoke software solutions developed by QVC for the control and data feed, and all workstations are connected with Quantel sQ servers as well as to a Quantum Stornext Scalar i2000 robotic LTO4 tape archive for long term storage. The Suitcase TV Purple logging system is used for regulatory compliance copies, both for off-air as well as program output, in addition to an in-house system for daily reviews of shows.
“We’ve implemented 3G-compatible equipment to future-proof the installation wherever possible, but as we currently operate at 1.5Gbps, all baseband flow is single link,” he adds.
MAM (Media Asset Management) and playout automation is managed by another bespoke QVC solution, developed by the Japanese software solutions company NSD on very specific requirements from the QVC Japan team – Bråhammar says the requirement was so specific that there was simply nothing on the market that would do the job. This includes approval and archiving processes (all editing suites and MAM clients have access to a low resolution proxy for off line editing, approval and viewing), seven hours of overnight playout, promo scheduling, and server automation for recording and playout of clips directly in the gallery.
“Overnight playout is normally ‘near to live’ so the rotation is very tight to match the on-air schedule, meaning that the validity time for recorded clips is very short,” he says. “We also produce and maintain a big clip library of product shots, demo clips and promos to complement live shows, which is all managed by our MAM system and stored in the Quantum deep archive.”
“We’ve carried out extensive tests of different downconverters and MPEG encoders, as well as fine-tuning the parameters, to get the best picture quality from the full chain. It’s a balancing act to get both graphics and normal moving pictures to look good at the same time. The choice of equipment across the whole chain, as well as correct alignment, is essential to get the best result – it’s as much of an art as a science, and certainly not a matter of ‘plug and play’!”